Airbus
Precision Components for Aerospace and Defence
The Customer
Airbus operates across a wide range of industries, from commercial aircraft and military transports to helicopters, satellites and space exploration. The company is also a key provider of data services, navigation and secure communications systems for clients worldwide. Through its Defence & Space division, Airbus supplies systems that support space travel, from individual electrical components to entire telecom relay platforms, satellites and manned spacecraft.
For over 25 years, Alroys has worked closely with Airbus’ Defence & Space division, providing precision-engineered components that play critical roles in their satellite systems. Our work with Airbus spans a broad range of custom components – cleats, heat shields and connector brackets – which are integral to satellite construction and operation.
The Brief
As a trusted supplier to Airbus, we are commissioned to produce several highly specialised components, including:
- Cleats: structural fittings designed to fasten and secure various satellite elements and equipment during space travel and deployment.
- Heat shields: vital for protecting sensitive satellite components from the extreme temperatures of space and re-entry, ensuring mission success.
- Connector brackets: critical for housing and protecting sensitive electronic connectors that ensure stable and reliable data transfer between satellite systems.
As with all components for aerospace and defence, our work for Airbus involves repeat products, whilst many are manufactured to the specific requirements of individual satellites.
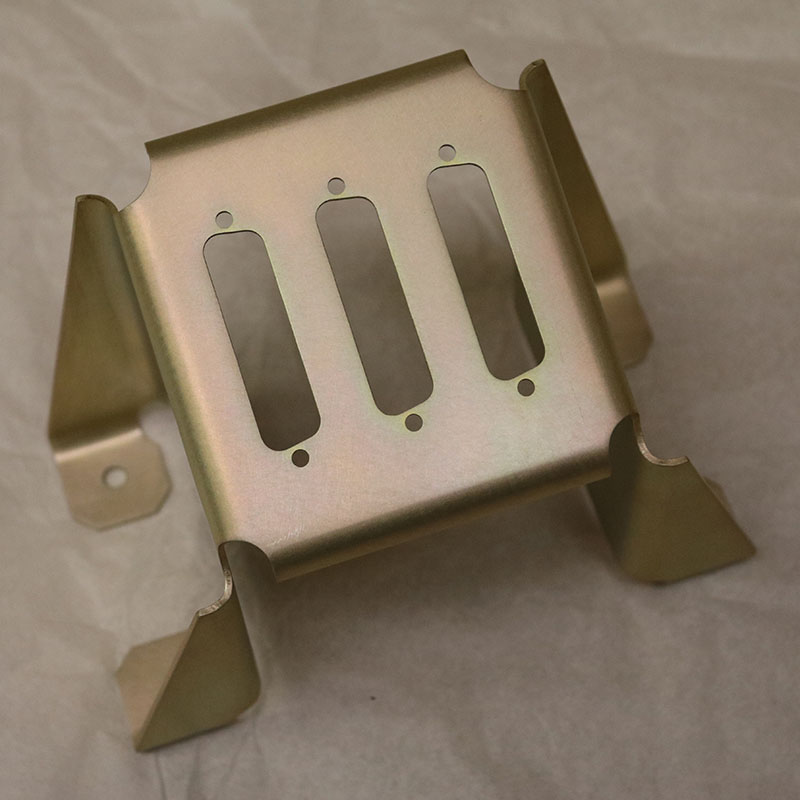
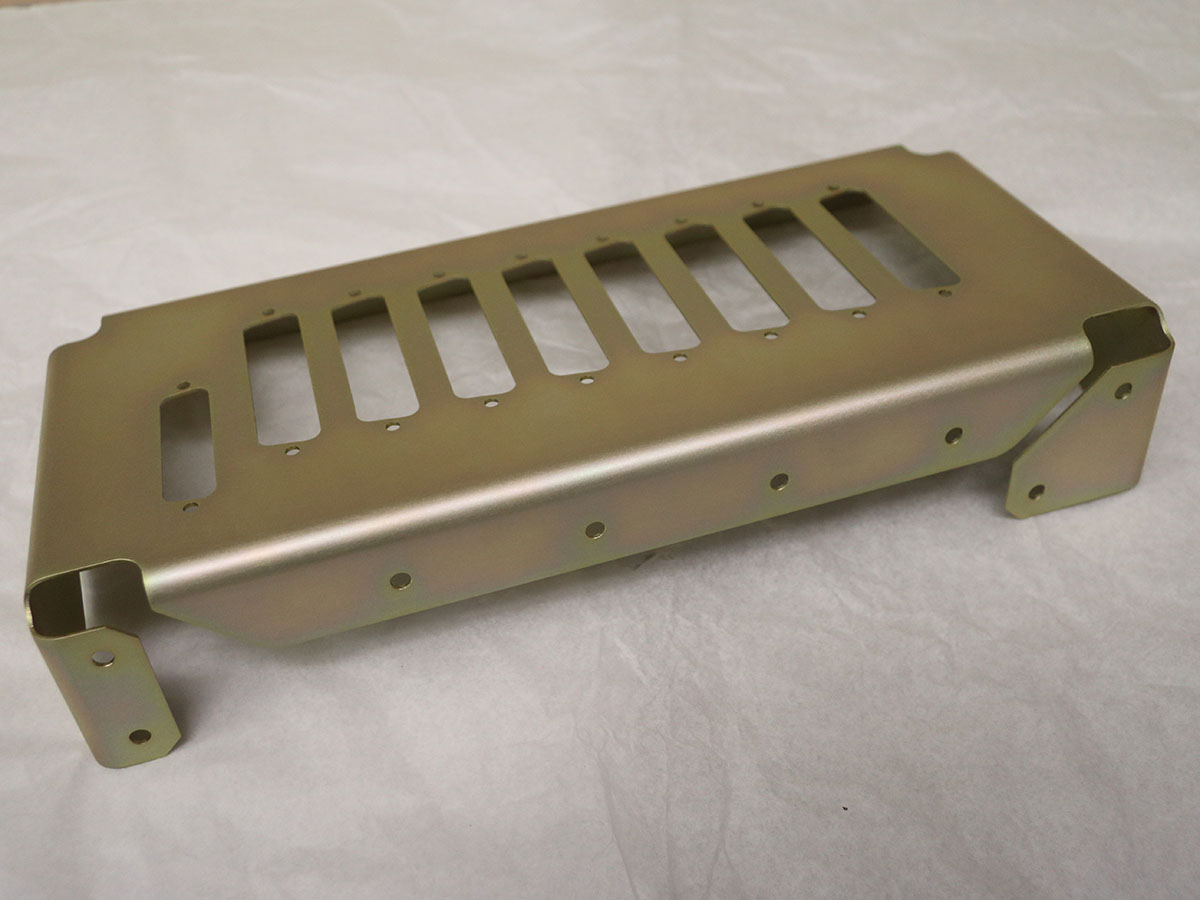
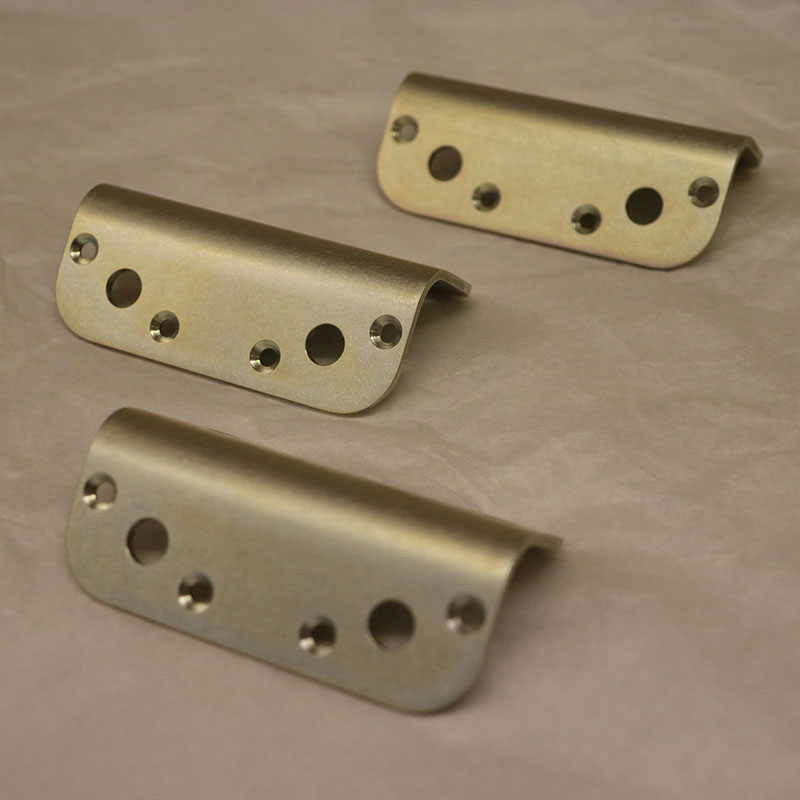
The Challenges
The nature of our partnership with Airbus involves overcoming a variety of challenges, from tight lead times to stringent design specifications and problem-solving. In particular:
- Stringent tolerances: components such as cleats and connector brackets must adhere to strict dimensional tolerances, often measured down to the micron. To achieve this level of precision, we rely on a combination of advanced CNC machining, precision tooling and rigorous quality control processes.
- Material selection: for each component, we work closely with the customer to select materials that can withstand the harsh conditions of space travel. For instance, heat shields – as the name implies – are made from materials that can endure extreme heat, such as aluminium. Components like cleats often use aerospace-grade aluminium alloys, while connector brackets favour titanium for its lightweight and non-magnetic properties.
- Complex geometries: many components, particularly connector brackets, require intricate designs involving multiple bends and precise placement of connection points. These geometries demand advanced forming, CNC bending, and welding processes to ensure exacting standards are met.
The Process
Precision machining
Once designs and materials have been approved, we proceed with precision CNC machining. Throughout production, components are inspected at each stage using high-precision metrology equipment to ensure dimensional accuracy. Given the tight tolerances required (as fine as ±0.01mm), some components necessitate skilled manual work, such as precision filing, reaming and re-measuring to achieve the perfect fit.
A particularly challenging component was a shield designed for a satellite, which needed to be as light as possible. Manufactured from 0.3mm thin aluminium, this shield posed significant risks during the CNC punching process, as the thin material could warp or cause machine failure. To overcome this, we backed the material with a thicker gauge of aluminium to provide structural support during punching, which was removed afterward. Additionally, we operated the CNC punch at slower speeds to achieve the precise outcome required.
Forming, welding and assembly
The required precision for components for aerospace and defence extends to bending and forming. Our CNC bending machines are employed to form cleats and connector brackets, maintaining tight tolerances. The heat shields, given their role in thermal protection, are fabricated with multiple layers of heat-resistant materials, requiring specialised assembly processes to ensure durability under extreme temperatures. We used TIG welding to join high-performance alloys, ensuring clean, strong welds that could withstand the rigours of space travel such as temperature variations.
Surface treatment and inspection
Once the components are machined, formed and welded, they undergo surface treatments for durability and corrosion resistance. Cleats and brackets are anodised, while heat shields receive a specialised coating for enhanced thermal protection. To ensure absolute reliability, each component is subjected to dye penetrant testing to detect any potential defects, such as hairline cracks.
Regulations and safety considerations
Results and Benefits
Our work with Airbus delivers exceptional result, the key benefits of which are:
- Custom engineering solutions: our ability to work closely with Airbus enables us to provide tailored solutions.
- Material expertise: our experience with aerospace-grade materials ensures optimal performance in extreme environments, from high levels of heat to intense mechanical stress.
- Precision and reliability: all our components for aerospace and defence are manufactured to tight tolerances, ensuring reliable performance in space conditions.
Alroys precision components for aerospace and defence
Alroys is proud to be an approved manufacture of components for aerospace and defence. Our expertise, commitment to quality, and ability to meet stringent industry standards, make us a trusted partner for aerospace and MoD projects.
If you have a project in the aerospace or defence sector, contact us today to learn how we can help deliver precision and reliability for your next mission.
Contact Us
Free Consultation
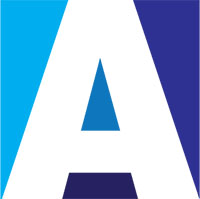
Talk to us about your next project
With over 60 years experience, we have built up a reputation of providing high quality products, on time delivery and professionalism.
As a leading steel manufacturer in the UK, we can handle any project using materials such as stainless steel or aluminium. Whether you come to us with a blank canvas or ideas already in mind, we will take on any request and contend to calculate and guarantee exceptional results.
Call us to discuss your next project.
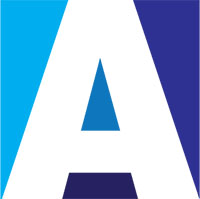
+44 01438 355687
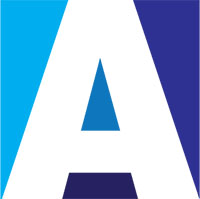
Arrange an appointment
If you’d like to visit us to discuss your next project in person, please use the number above to arrange a time suitable for you.
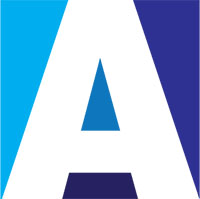
Download our brochure
Click here to download our brochure.
Depending on your browser settings, the brochure will either open in a new browser window (save to your computer to view) or will download directly to your computer. You will require a pdf reader to view our brochure once saved to your computer.