Different types
of metals and their applications
There are many different types of metals in existence, from which there are various grades to choose. Metal accounts for 75% of elements in the periodic table. Metals such as iron, steel, copper, bronze, brass, aluminium, titanium and lead feature in our daily lives in thousands of different applications.
Although metals share similar properties, the suitability of one over another will depend upon the intended application. There are quite a few properties to consider: melting point, ease of machining and welding, strength, durability, aesthetics, temperature tolerance, thermal and electrical conductivity and, of course, cost.
These properties and characteristics are dictated by whether a metal is ferrous or non-ferrous (indicating the presence of iron) and / or the addition of other pure metals (to create alloys). The classification of metals is, therefore, a valuable means of selecting the right one for a particular application.
This blog looks at the different types of metals available, and why they are chosen for specific applications.
Classification of metals
The two main classifications for metal are by iron content or atomic structure:
Classification by iron content
Whether or not a metal contains iron is the most common method of classification. This makes it a ferrous metal, such as steel, cast iron, wrought iron. The iron imparts magnetic properties to the metal and also makes it prone to corrosion. Those metals without iron content do not possess any magnetic properties and are termed non-ferrous metals. Examples include aluminium, lead, brass, copper and zinc.
Classification by atomic structure
Metals are also classified on the basis of their atomic structure as defined in the periodic table. (See the Royal Society of Chemistry for a brilliant interactive app.) These metals are further classified as alkaline, transition, or alkaline earth metal. Metals that belong to the same group tend to behave in similar ways such as being low-melting and tarnishing when exposed to air.
Categories of metal
When we use iron content as our guide, metals are divided into three categories: ferrous, non-ferrous and metal alloy.
Ferrous metal
Almost 90% of manufactured metals are ferrous metals – steel, for instance. The word ‘ferrous’ comes from the Latin word ‘ferrum,’ which means ‘iron.’ Ferrous metals include steel, cast iron, as well as alloys of iron with other metals (such as stainless steel). Characteristics include:
- Durability
- Tensile strength
- Electrical conductivity
- Low corrosion resistance
- Recyclable
- Usually magnetic
- Silver in colour
Ferrous metals, such as cast and wrought iron or carbon steel, are known for their tensile strength and durability. As a result, they are widely used in the construction industry providing the structure for bridges and skyscrapers. Ferrous metals are also found in shipping containers, pipework, automobiles, railways and a range of both commercial and domestic tools.
The high carbon content of most ferrous metals means that they are vulnerable to rust. Wrought iron is an exception to this as its purity gives it a resistance to corrosion. Alloying elements will make a steel more resistant to rusting when exposed to moisture. For example adding chromium to create stainless steel.
Ferrous metals have been in use for thousands of years and have a huge range of different applications, from the largest structures to the smallest nuts and bolts. Since most ferrous metals are magnetic, they are often used in electrical and motor applications.
Non-ferrous metal
Non-ferrous metals are alloys or metals containing zero (or very little) iron. They tend to be more expensive than ferrous metals due to their lighter weight. Other attributes include:
- Non-magnetic properties
- Easy to fabricate (including machinability, casting and welding)
- High resistance to corrosion
- Good thermal and electrical conductivity
- Low density
- Non-magnetic
- Colour range
Non-ferrous metals are usually obtained from minerals like carbonates, silicates and sulphides before being refined through electrolysis. They include aluminium, copper, lead, nickel, tin, titanium and zinc, as well as copper alloys like brass and bronze. Other rare, or precious, non-ferrous metals include gold, silver, platinum, cobalt, mercury, tungsten, lithium and zirconium.
Non-ferrous metals are used for a wide range of commercial, industrial and residential applications. Some, such as aluminium or titanium alloys, can replace steel. However, they are often more expensive and are better employed for their specific attributes. Being softer and more malleable, non-ferrous metals such as gold and silver can be used in more aesthetic settings.
Metal alloys
Metal alloys are a combination of more than one element including another metal. For example, brass is an alloy of two metals, copper and zinc. Steel is an alloy of a metallic element (iron) and around 2% of a non-metallic element (carbon).
Alloying a metal is a means of enhancing a specific property. Each substance within the alloy contributes something different to the mix, creating a unique product that is harder, more durable, more resistant to corrosion or has increased load-bearing capabilities. Consequently, they are in high demand in a variety of applications and industries such as manufacturing, electronics, domestic goods, architecture, plumbing, and the automotive and aerospace industries.
Iron and its alloys and their properties
In modern society iron is the most important of all metals. As approximately 5% of the earth’s crust is iron, so it’s also very easy to find.
The basic, raw metal is pig iron which can be further refined to obtain pure iron which, though stronger than other metals, is not resistant to corrosion. It’s also extremely heavy due to its high density. Adding carbon to iron (creating carbon steel) alleviates some of these weaknesses. It’s the ability to create so many different types of steel that makes iron so important in our lives – from paperclips to skyscrapers.
Different types of metals
Here’s just some of the metals most commonly used:
Iron
Iron is the most commonly used and cheapest metal. There are three types: pig iron, cast iron and wrought iron.
Pig iron: a crude form of iron, used as a raw material for the production of various other ferrous metals, such as cast iron and steel.
Cast iron: created by melting pig iron with coke and limestone. Cast iron tends to be brittle and is notoriously difficult to weld. However, it is an ideal engineering material with a wide range of applications particularly in the automotive industry. This is due to its relatively low melting point, castability, excellent machinability and resistance to both deformation and wear.
Wrought iron: tough, ductile and corrosion-resistant, wrought iron is a type of highly purified metal, with small amounts of silicate slag moulded into the filaments. This means it is ideal for forging into products such as guard rails, gates and garden furniture. However, mild steel (see below) has more or less replaced wrought iron.
Steel
Steel is an alloy made up of several chemical elements, together with iron and carbon, to create a strong and fracture-resistant metal. Its high tensile strength and low cost makes it the most widely used material for an incredibly diverse range of products: from buildings, weaponry and machines, to electrical equipment and all manner of instruments.
Carbon steel: defined as a basic steel containing carbon and iron, with other elements sometimes added in very small amounts. These alloying elements include manganese, vanadium, chromium, nickel and tungsten. Variously, they alter strength and resistance to abrasion and wear, and affect electrical as well as magnetic properties. Used for pipework, especially for energy-related applications, it’s an extremely common type of metal because it remains relatively cheap to make.
Carbon steel is divided into low, medium and high (for example plain-carbon steel, low-carbon steel and mild steel, which has pretty much replaced wrought iron). The higher the carbon content, the harder and stronger the steel while less carbon creates a softer, cheaper metal.
Stainless steel: stainless steel contains a high amount of chromium, which makes it 200 times more corrosion resistant than mild steel. Its a highly-valued metal where hygiene and high levels of cleanliness are important – such as operating theatres, dental surgeries and kitchens.
Copper
Copper is a soft, malleable and ductile metal with a reddish-brown appearance. It provides good conductivity of electricity, can be cast, forged, rolled and drawn into wires. It is used extensively for wire, coins and household utensils.
Bronze
Bronze is mostly made up of alloys such as copper and tin. It’s a comparatively hard metal, resist ant to surface wear and corrosion, and can be easily shaped or rolled into wires, rods, and sheets. Bronze can be more easily melted and, cast – especially for art works such as sculpture. Aluminium bronze (copper and aluminium) is particularly strong, and often cast, or forged, in pipe fittings, pumps, gears, ships and turbine blades.
Brass
Brass comprises copper and zinc alloy. There are different types of brass, depending on the ratio of copper to zinc, and by adding small amounts of other elements. Brass is stronger than copper but has a lower thermal and electrical conductivity. Its also very resistant to atmospheric corrosion and can be easily soldered. Common applications are locks, gears and valves.
Aluminium
Aluminium is a lightweight metal which, when mixed with small amounts of other alloys, becomes hard and rigid. Then it becomes very versatile because it’s durable, electrically conductive, and corrosion resistant. Aluminium is easy to machine and does not magnetise. Widely used for overhead cables, aircraft and automobile parts, aluminium also has considerably aesthetic qualities. It’s lightweight plus the wide variety of surface finishes and colours available make it a popular material with architects.
Titanium
Titanium is an important engineering metal because it’s lightweight and strong. It also has high thermal stability, even at temperatures as extreme as 480°C. For these reasons, titanium is widely used in the aerospace industry. Titanium is also popular for military equipment, sporting goods, the chemical industry. Finally, its resistance to corrosion makes it ideal for medical purposes.
Lead
Lead is heavy in weight with a relatively low melting point. Since it is a soft metal (it can be easily cut with a blade) and malleable, it has no tenacity. Lead is generally used for soldering, as linings for acid tanks, cisterns, water pipes, and as coating for electric cables.
Periodic table of metals
The periodic table organises chemical elements according to increasing atomic number. Chemical elements are the basic substances that make up all matter and each one has a particular feature called its atomic number derived from the amount of tiny particles (protons) contained in each atom. The periodic table arranges the elements in rows (order of atomic number) and columns (grouping elements with similar chemical properties). For example, certain gases are in one column and metals are in another.
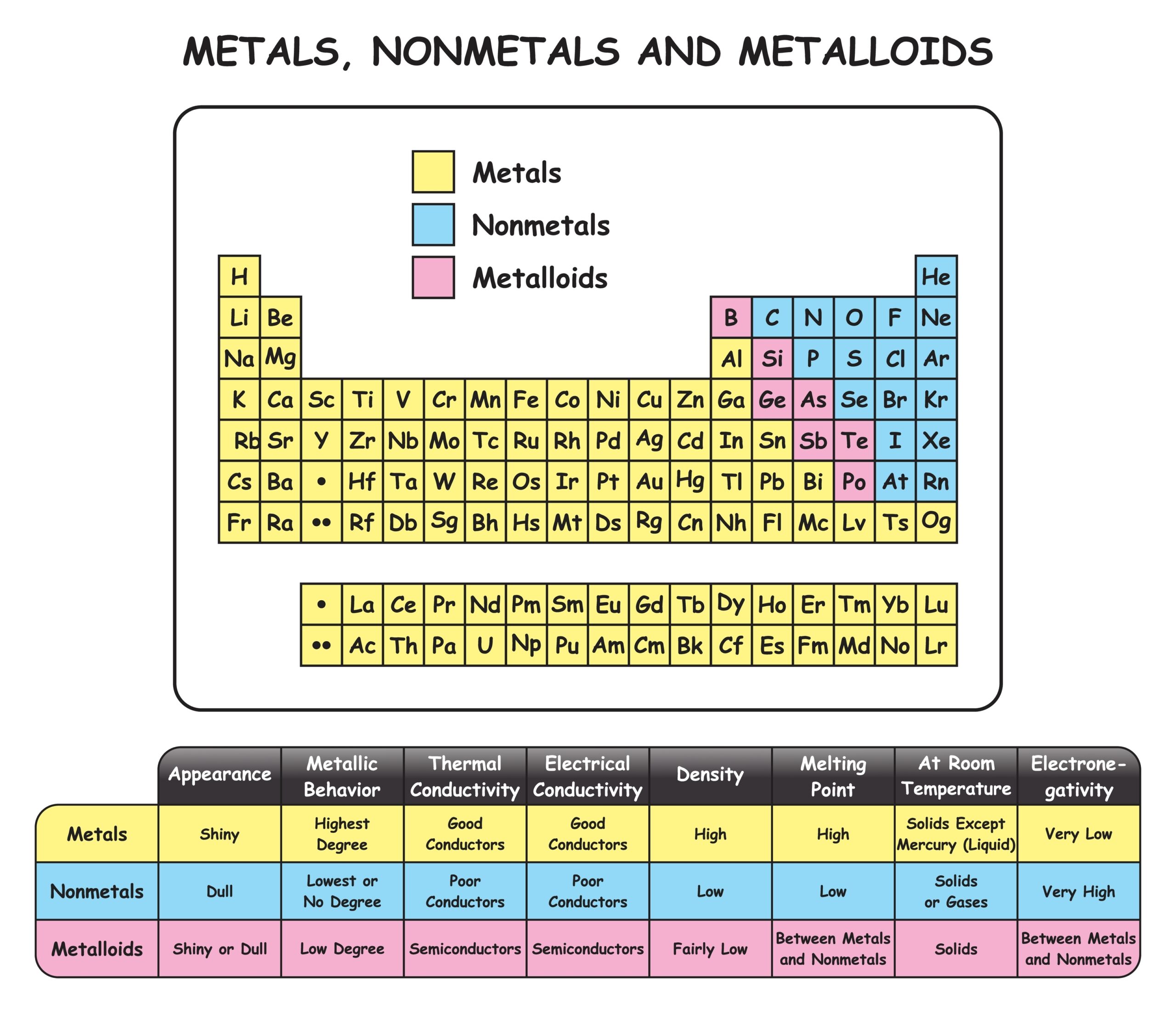
Over 75% of the elements on the periodic table are metals
Essentially, the periodic table helps chemists, physicists and engineers make decisions about the elements and their properties, such as weight and electronic configuration.
Different metals for different applications
Metal is hugely important in our lives, and choosing between the many different types of metals and their applications takes skill and knowledge. The nature of your project and the objectives you are seeking to achieve, will dictate the properties you need and the priority you set for them: melting point, ease of machining and welding, strength, durability, aesthetics, weight, temperature tolerance, thermal and electrical conductivity and, of course, cost.
Find out more about our sheet metal services , or call us to discuss your metal projects and the applications you are planning.