Bespoke aluminium brise soleil
Elegant and functional aluminium brise soleil
Alroys was asked to create an aluminium brise soleil by our customer, Vernier. The brise soleil (literally ‘sun blocker’ in French) was part of a project Vernier was managing for property investor and developer, Arlington.
An architectural feature, a brise soleil is most commonly used to prevent façades, with a large amount of glass, from overheating. It comprises vertical or horizontal aluminium supporting struts set at precise angles to accommodate the movement of the sun. It’s not a new technique; Le Corbusier used it in 1948 for a combined surgery and home in Argentina. It is, however, a highly effective way of reducing heat from the sun in a building.
In this case, the brise soleil was needed to shade foot passengers from the sun on a new bridge link between two buildings. It also had to match an existing brise soleil, used on the two buildings either side of the bridge.
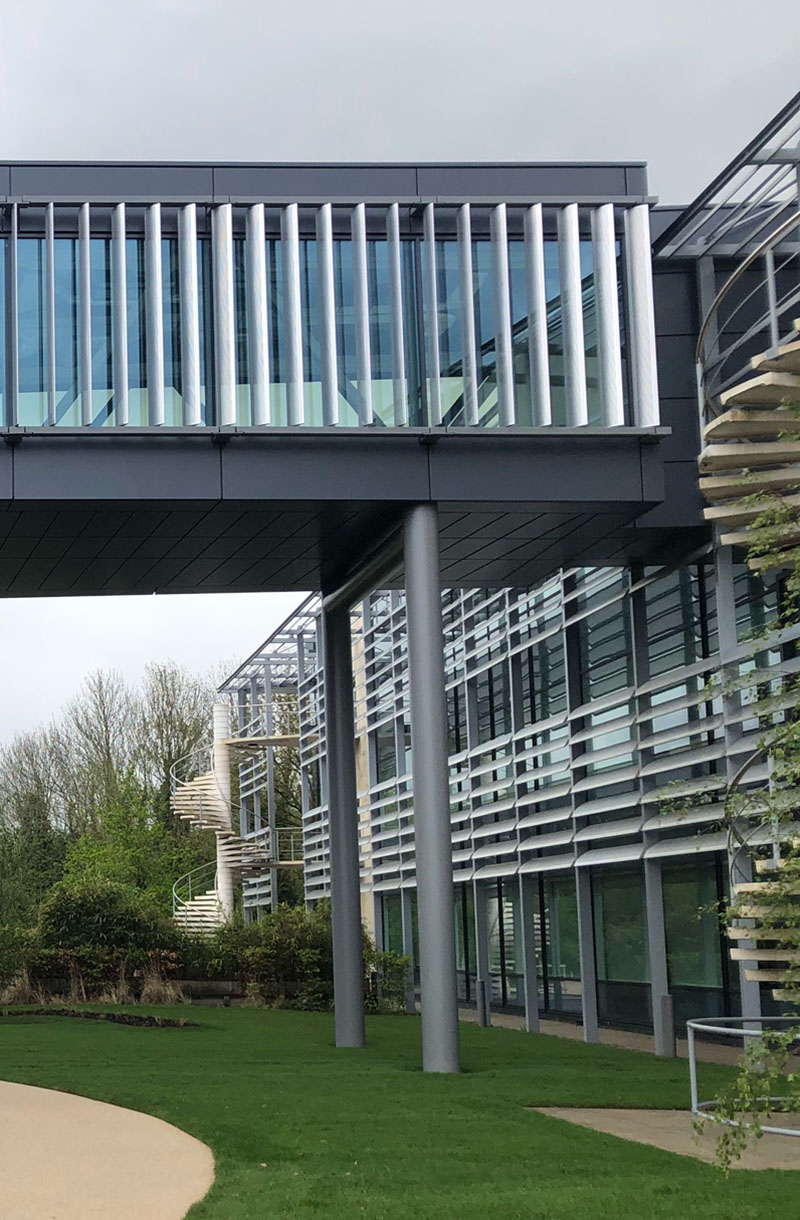
Alroys created a brise soleil that matched the existing structure on the buildings either side of the bridge.
Getting the brise soleil design and spec right
The brise soleils on the existing buildings were built 30 years ago, and as no accurate drawings could be found, we visually matched for our new bridge version.
Creating the bespoke brise soleil in aluminium, involved designing and sourcing special extrusion tooling and anodising:
Bespoke extrusion tooling for the aluminium brise soleil
Before we committed to having the extrusion made, we milled a sample profile. The minimum run of 1 ton, together with the cost of the bespoke tooling (approximately £2,000), meant we wanted to be sure of matching the customer’s brief before committing to the cost of production.
Anodising the aluminium struts
Although aluminium doesn’t rust, it does get stained if exposed to the elements which was inevitable in this case. Anodising protects aluminium and gives it a clean finish – in this instance, a satin finish was chosen.
We carefully researched and sourced the right anodising solution. For a start, we needed an anodising company that could accommodate our project; at 3m, our struts exceeded the usual length of aluminium to be anodised (2m).
Anodising is like etching in that it creates a film on the surface, measured in microns according to the thickness of the metal. Although 25-30 microns matched our spec, we were advised that this level would not necessarily give better protection for external use. So we chose 20-25 microns for long-term resistance to environmental conditions, which also worked out to be the most economical option.
Image: We milled a sample aluminium strut to ensure it met the brief.
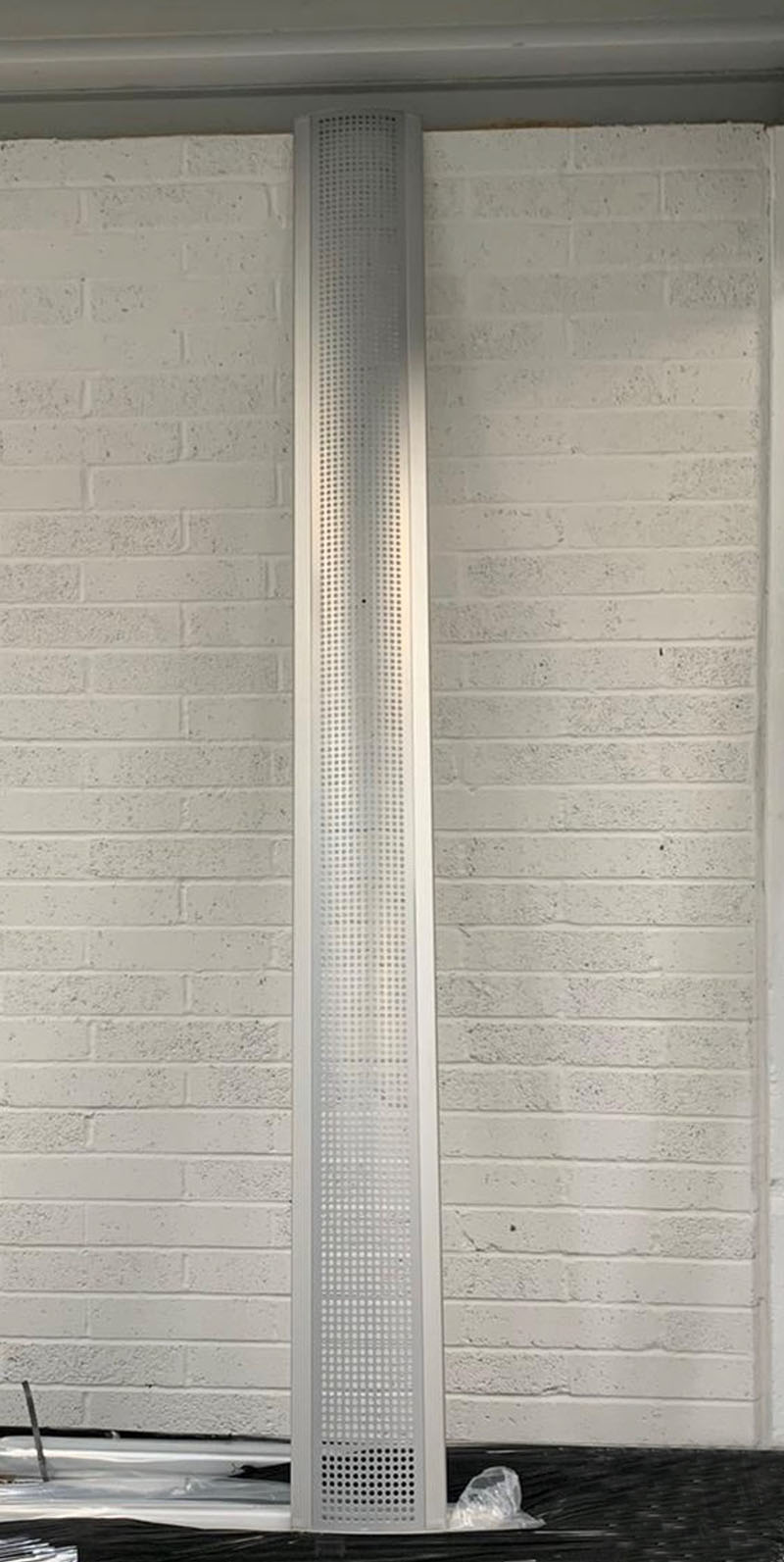
Additional tasks for the bridge link
The client entrusted two other tasks to Alroys, both of which were critical to the success of the bridge link:
- Creating skylights in the roof of the bridge for the air con: this required complicated brackets to ensure the roof remain supported. The brackets accommodated differently-angled beams so each one (there were 16) was a unique shape.
- Connecting the bridge to the two buildings: this was another painstaking part of the project because the bridge link was smaller than the openings on both buildings. Glass panels at the end of each building were removed in order to connect the bridge. Then, around the edges, we fitted waterproof infill panels to join the buildings to the bridge. Having taken careful site measurements, we created bespoke panels that fitted perfectly, accommodating the variance in thickness of the panels at either end of the existing buildings.
Installing the bespoke brise soleil
Once again, accurate site measurement ensured a perfect fit for each of the 49 aluminium panels that made up the brise soleil. We also drilled the holes at the top and bottom to ensure perfect alignment when they were fitted to the beams by another contractor.
Finally, we created a manual for removing and reinstalling both the aluminium struts and glass panels should this ever become necessary (eg for maintenance). This included a full pack of drawings and CofCs (certification of conformity) from the manufacturers.
Good communication is key to successful fabrication projects
This project, like many we get involved in, required Alroys to apply our knowledge and skills in different ways. Problem-solving and research is always part of the brief, and we take the same robust approach to ensuring good practice each time. Working out the ‘what ifs’ and ‘how abouts’ each time is really important, particularly when we are faced with something new or unknown. It’s the old fashion ‘belt and braces’ approach.
As far as the customer is concerned, they need reassurance and regular updating on progress. That’s how we build trust and ensure a good relationship. We communicated regularly and comprehensively throughout the brise solei project. In turn, this meant that Vernier could also report positively on the progress of the project to their client.
Our customers have faith in our work, and take our advice because they know we’re experienced fabricators and diligent problem-solvers. So, when we say “that won’t work but this will”, our customers take our advice. Consequently, we’re delighted to report that the brise soleil is another successful project for Alroys.