How to achieve repeatability and accuracy with CNC bending
Like all our fabrication and component work, it starts with understanding the purpose of a project and the role CNC bending plays in production. Can we improve on functionality, production time or cost? Is what our customer wants achievable, let alone economical? If not, what can we recommend as an alternative or work-around? Our skill and experience means we understand the extent of the CNC bending machine’s capabilities and the characteristics of the materials being used.
Here’s a brief insight to how we approach the CNC bending aspect of a project:
Achieving the desired outcome through intelligent CNC bending
Uppermost in our mind is ensuring every project benefits from our knowledge and experience. Sometimes a customer has seen something but not realised the implications of replicating it – the need for fancy tooling or a time-consuming process will impact on cost. Other times, designers aren’t aware of other options so we introduce them to different ways of achieving the same – or better – outcome:
- The ‘difficult’ spec: such as a 4ml flange on 2ml material: increasing the flange to 8ml makes the job easier which is a good thing whichever way you look at it.
- Folds close together: a specific joggle tool will enable you to achieve 2 closely-situated folds simultaneously. But it’s not a standard tool so, unless the project justifies this kind of specialist attention (eg large quantities), we’d advise an adjustment to the design to bring the project back into a more acceptable cost range.
- Short fold, massively thick material: usually physically impossible (try bending a thick directory) so this could be a job for fabrication (eg welding parts together rather than bending one single part).
- A circular tray – ‘spinning’ is a solution to force the flange into shape but it’s time-consuming. So, if the budget can’t accommodate this kind of specialist treatment, 2 options are: weld the flanges or choose a square / rectangular shape for the tray.
Understand how a material reacts to being bent
The CNC bending machine is accurate – assuming its well maintained, tonnage is observed (see below), etc. However, materials react differently to forming. Mild cold-rolled steel forms with less tonnage than stainless steel but more tonnage then 5052 H32 aluminium. Stainless has more springback than cold-rolled steel. Cold-rolled is anisotropic meaning bending angles, forming tonnage and the floated inside bend radius can change depending on the relationship to the material’s grain direction – all of which affect the end result. Essentially, how a material reacts to being bent determines the process you choose in order to achieve the most successful outcome.
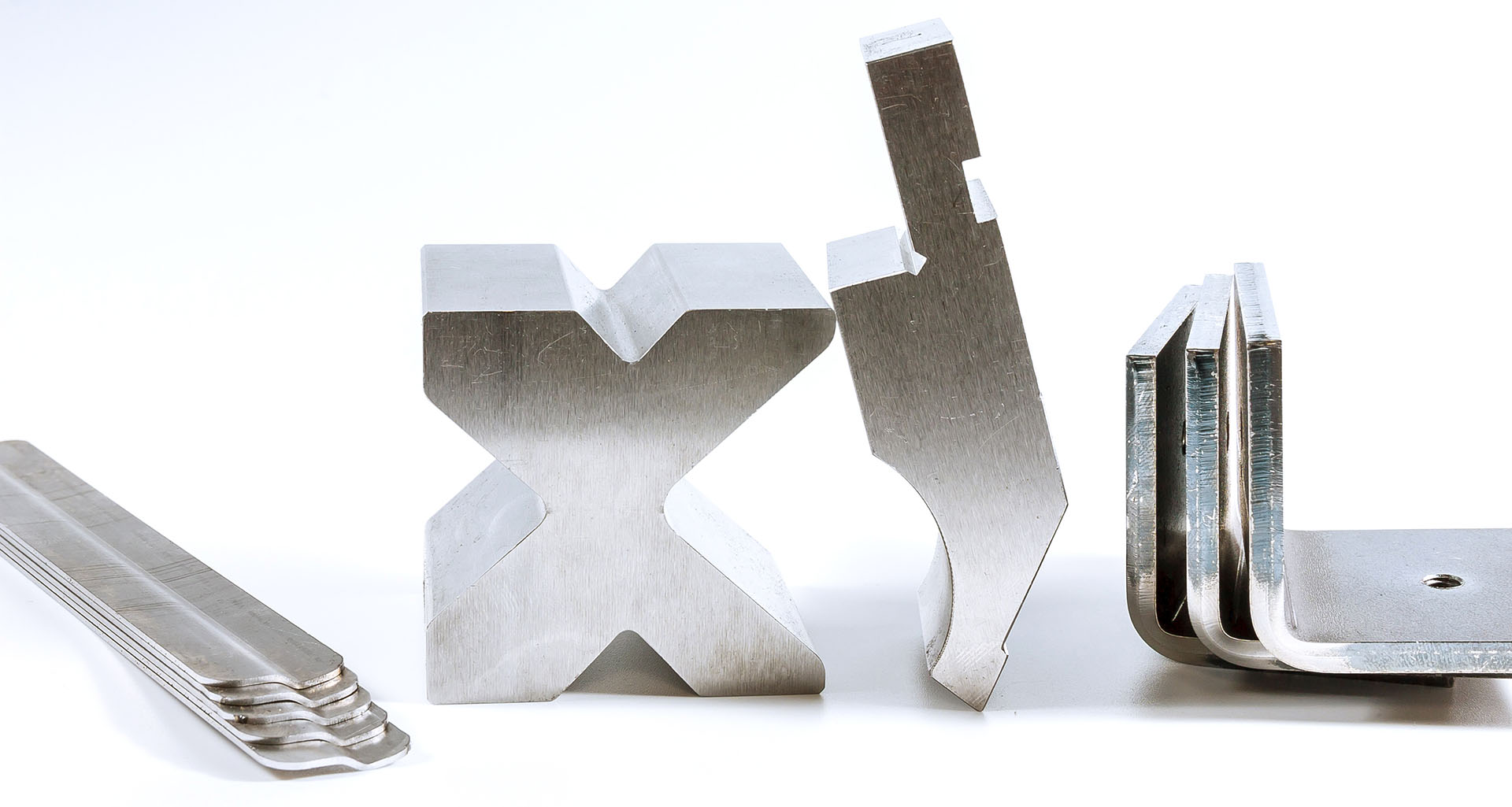
Checking the direction of the grain
To predict the material’s behaviour accurately during bending you need to factor in the grain.
Bending with the grain limits how tight an inside bend radius can be achieved without cracking the outside of the bend. Bend angles also can be less consistent. However, an advantage going with the grain is it takes less pressure to make the bend.
The direction of the grain also affects the amount of springback you can expect. At the end of the forming process, parts spring back when released thereby affecting the dimensional accuracy of a finished part.
Inconsistencies across different batches
Ideally you work from the same batch but this isn’t always possible, especially if you’re bending a high production run of components.
Variation in material thickness is, for example, highly likely. The thickness of each batch may be within the material spec but, when it comes to bending, even just 0.05mm difference will affect cumulative tolerances.
Quality control in CNC bending
Quality control is being vigilant – knowing what you’re looking for and when. Even with a single fold, ongoing checks and adjustments are important so you can see how the material is behaving and, if necessary, spot any issues quickly – particularly keeping within your tolerances.
With multiple folds, the need for vigilance is even greater because of cumulative tolerances. If you don’t correct as you go along, the adjustment at the end may be too large to make in order to get back within your tolerance range. With an 8-fold project, for example, you may not even be able to fold all 8 in one go. Instead, changing the set up and folding 2 at a time could be a better option. There will undoubtedly be cumulative errors so check the first folds.
The aim is not to snooker yourself and compromise the project! Quite apart from not meeting the design brief, you’ll have timing and costing issues to manage. So plan ongoing checking and adjusting while you bend.
Then, we adopt one of two final quality control approaches, depending upon the requirements of our customer:
- 100% inspection: checking every single fold on every single component.
- First article inspection: despite the name, the inspected article may not necessarily be the ‘first’ produced but a sample from the first production run provided to the customer.
Success with CNC bending gets back to tooling
In many ways, the success with CNC bending gets back to tooling. Using the wrong tooling is one of the leading causes of errors with CNC bending. Selecting the wrong tool may create the wrong radius which changes the bend deduction and causes the final part to be incorrect. Then there’s the safety aspect. Like the press brake itself, tools are rated to handle only so much forming tonnage. Too much tonnage can damage or destroy a tool, create safety hazards, even damage or destroy the press brake itself.
Getting the tooling right for CNC bending and you’re well on the way to meeting your customer’s objectives.