What is CNC Punching and How Does it Work?
As the name implies, Computer Numerical Control (CNC) punching is a very reliable means of literally ‘punching’ shapes in sheet metal using a programmable machine. The programme creates a precise range of co-ordinates to punch the required shape. This delivers accuracy and cost-efficiency for both small batch work and long production runs.
Unlike a laser, a punching machine can also complete formed features and profiles such as countersinks, beads, and louvres with high accuracy and speed.
In answering the question ‘What is CNC punching?’, this blog explores how it works, its advantages and the type of machines available to you.
How does CNC punching work?
The CNC punching programme moves the sheet metal in an ‘X’ (left and right) and ‘Y’ direction (in and out) so it’s precisely positioned under the machine’s punching ram. This then forces down the tooling to ‘punch’ an accurate hole or shape into the material which is clamped firmly in place.
The programme ensures an efficient use of material, reducing waste, and therefore cost. Laying out the patterns of components accurately will reduce the punching time and the amount of waste involved. The idea is to produce as many parts from as little material as possible. It’s called ‘nesting’.
Types of CNC machines
There are two types of CNC punching machine:
1. A multi-tool (or ‘mould’) turret design as manufactured by Armada
2. A single linear / rail magazine of tools, eg the Trumpf brand
Turret style CNC punching machine
The turret style machine holds all of the tools in a circular turret, each tool remaining in a set position. Three-four rotational tools are positioned in an index station. Having 60+ tools available enables you to easily and quickly create multiple shapes, both simple and complex.
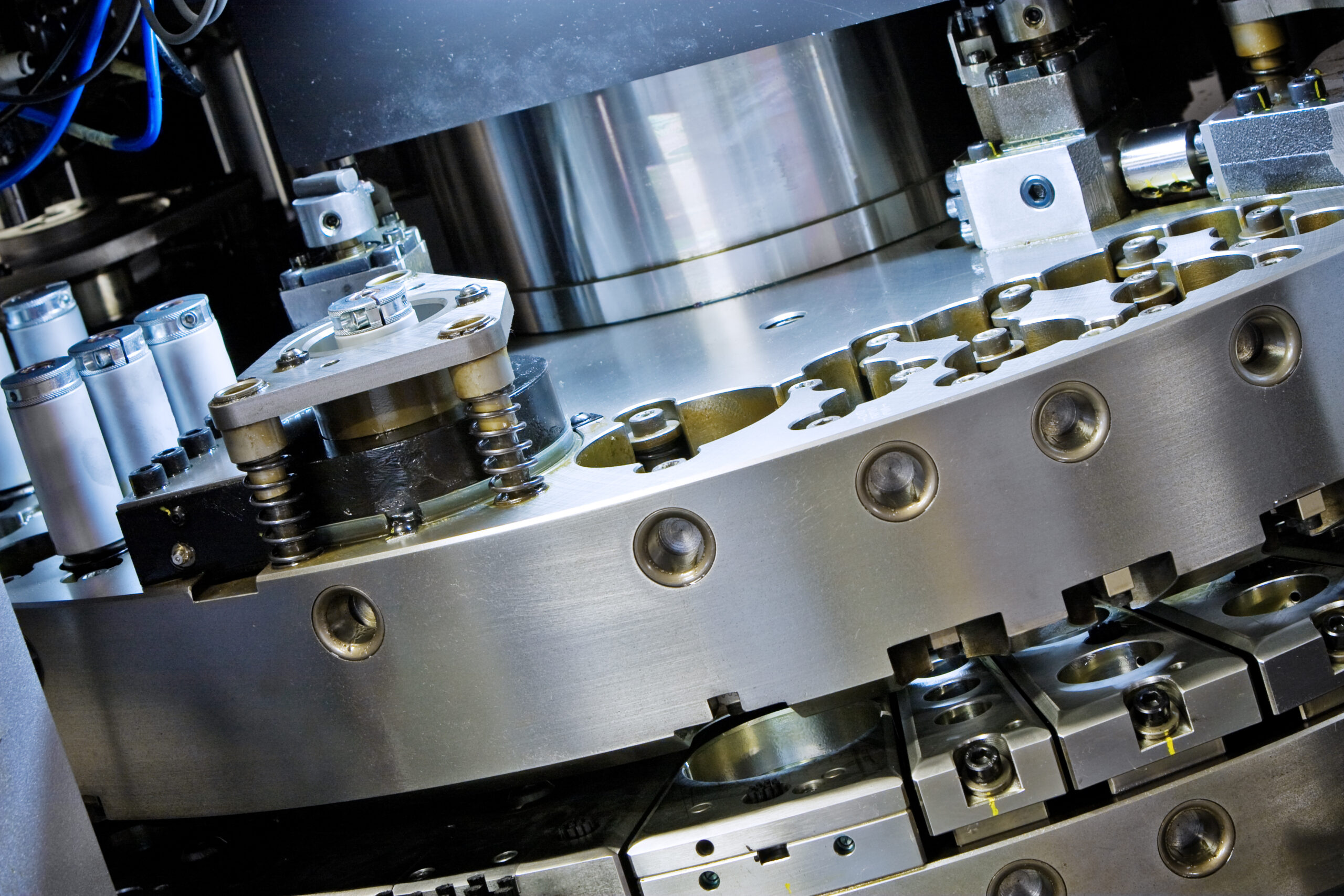
Turret style CNC punching machine
Linear rail style CNC punching machine
The linear style magazine means one tool at a time is loaded into the punching head allowing for full rotation for each tool. An advantage is the concurrent set up between jobs with minimal change over time.
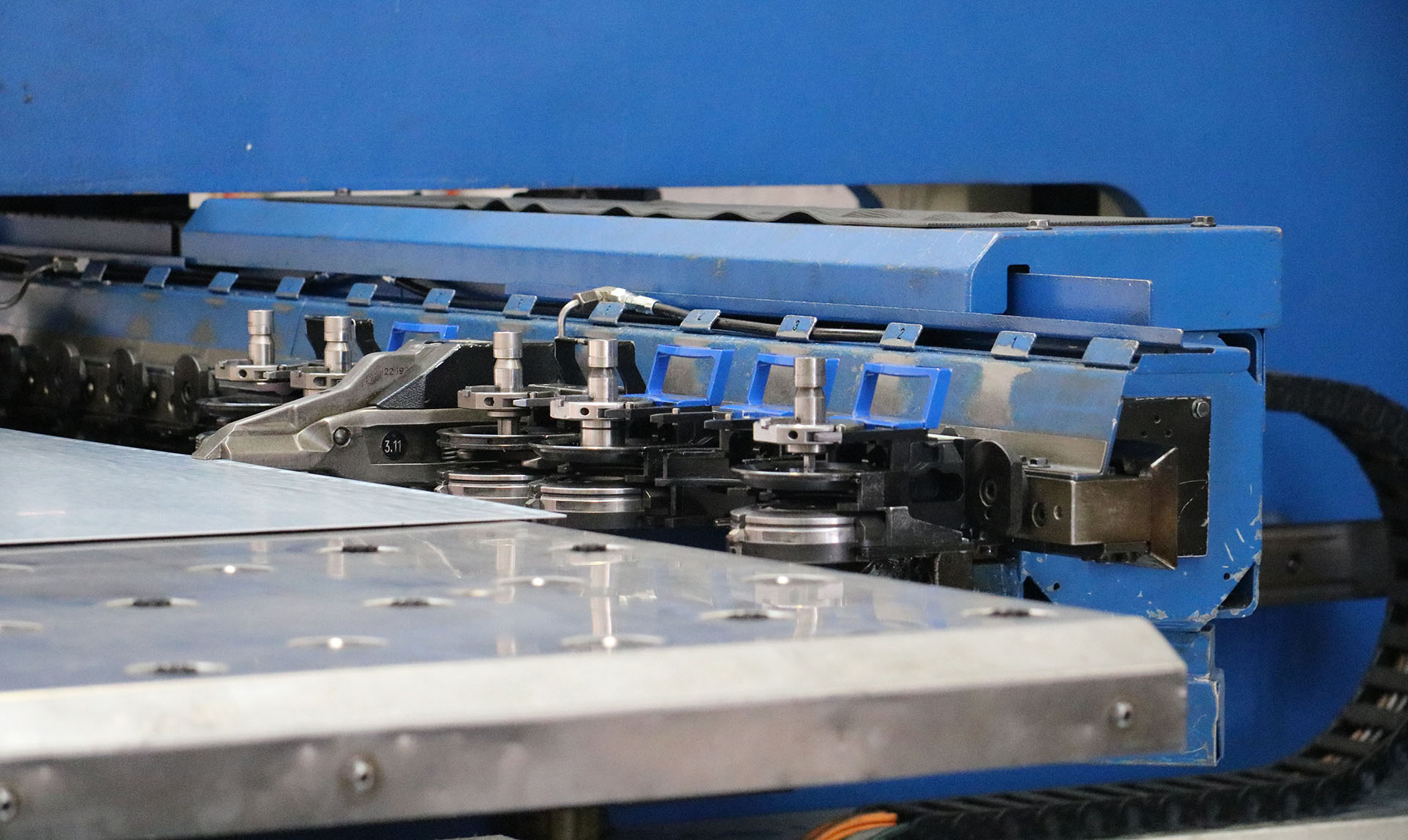
Linear rail style CNC punching machine
Linear rail style CNC punching machine
The linear style magazine means one tool at a time is loaded into the punching head allowing for full rotation for each tool. An advantage is the concurrent set up between jobs with minimal change over time.
What can CNC punching create?
We use CNC punching for customers working in various industries such as automotive, aerospace, construction and architectural sectors. We can create a range of useful features quickly and economically. For example, louvres for air vents, dimples for locating positions, bridges for slide rails or back stops. It also delivers an impressive hit rate which means it’s ideal for perforated parts, such as grilles. Using cluster tools we can punch a number of holes in a grid at the same time thereby drastically reducing run times. This can be used very effectively for ventilation grilles or LED panels.
Advantages of CNC punching
The advantages of CNC punching can be summed up in just two words: cost effectiveness. It’s a fast and accurate means of using material efficiently. We achieve excellent production run times (eg 500 punch strokes a minute) and a high level of precision, regardless of the complexity of the design.
However, CNC punching is at its most economical when producing simple shapes in larger volumes. For example, apertures such as holes, squares and obrounds as well as more sophisticated shapes like countersinks, louvres, dimples and locking tabs. With custom tooling, we can even incorporate folds thereby creating an entire part. Cluster tools, on the other hand, can be used to punch large grid patterns, creating multiple holes and slots in a single punch stroke.
What can CNC punching create?
We use CNC punching for customers working in various industries such as automotive, aerospace, construction and architectural sectors. We can create a range of useful features quickly and economically: louvres for air vents, dimples for locating positions, bridges for slide rails or back stops. It also delivers an impressive hit rate which means it’s ideal for perforated parts, such as grilles. Using cluster tools we can punch a number of holes in a grid at the same time thereby drastically reducing run times. This can be used very effectively for ventilation grilles or LED panels.
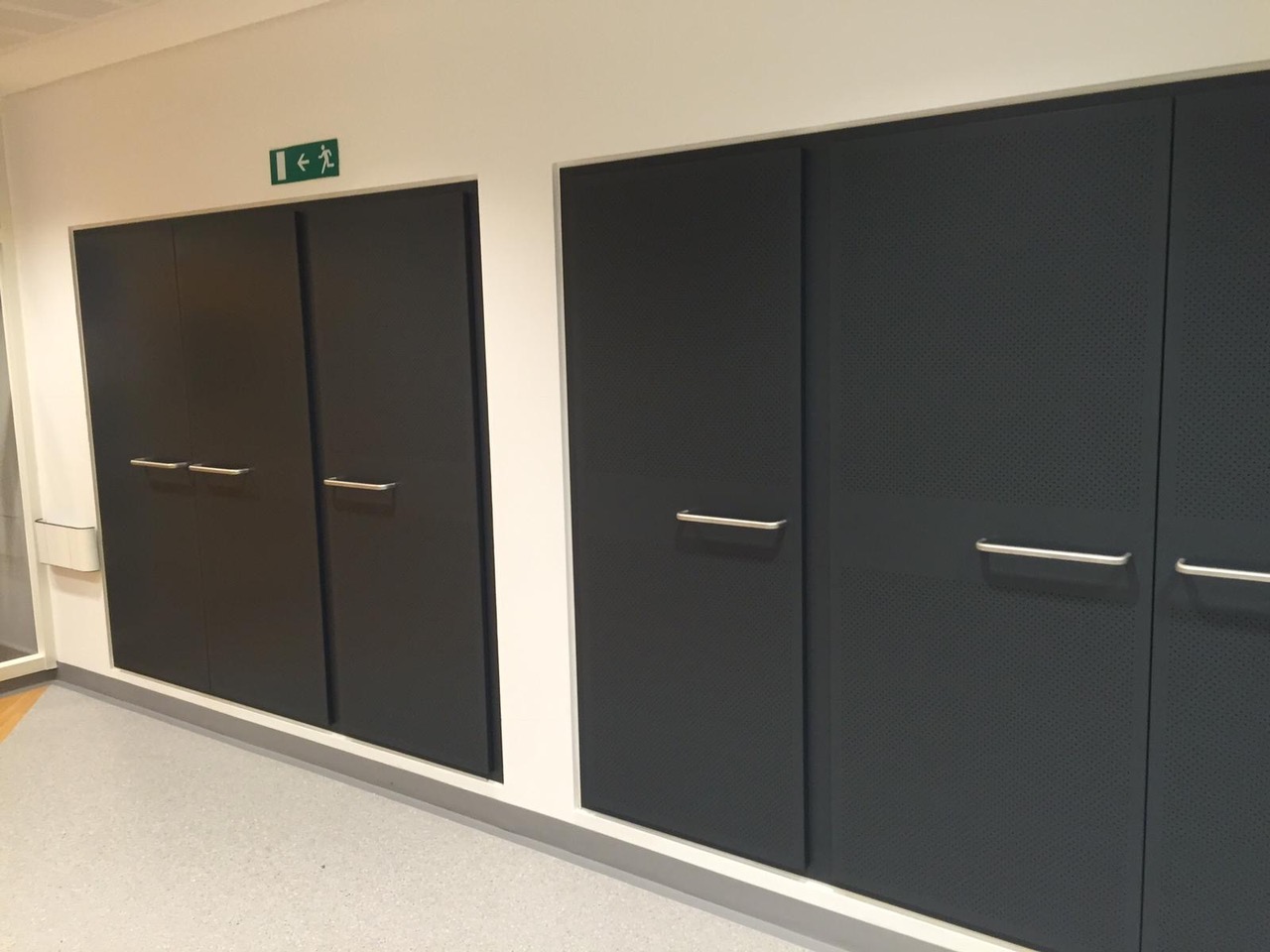
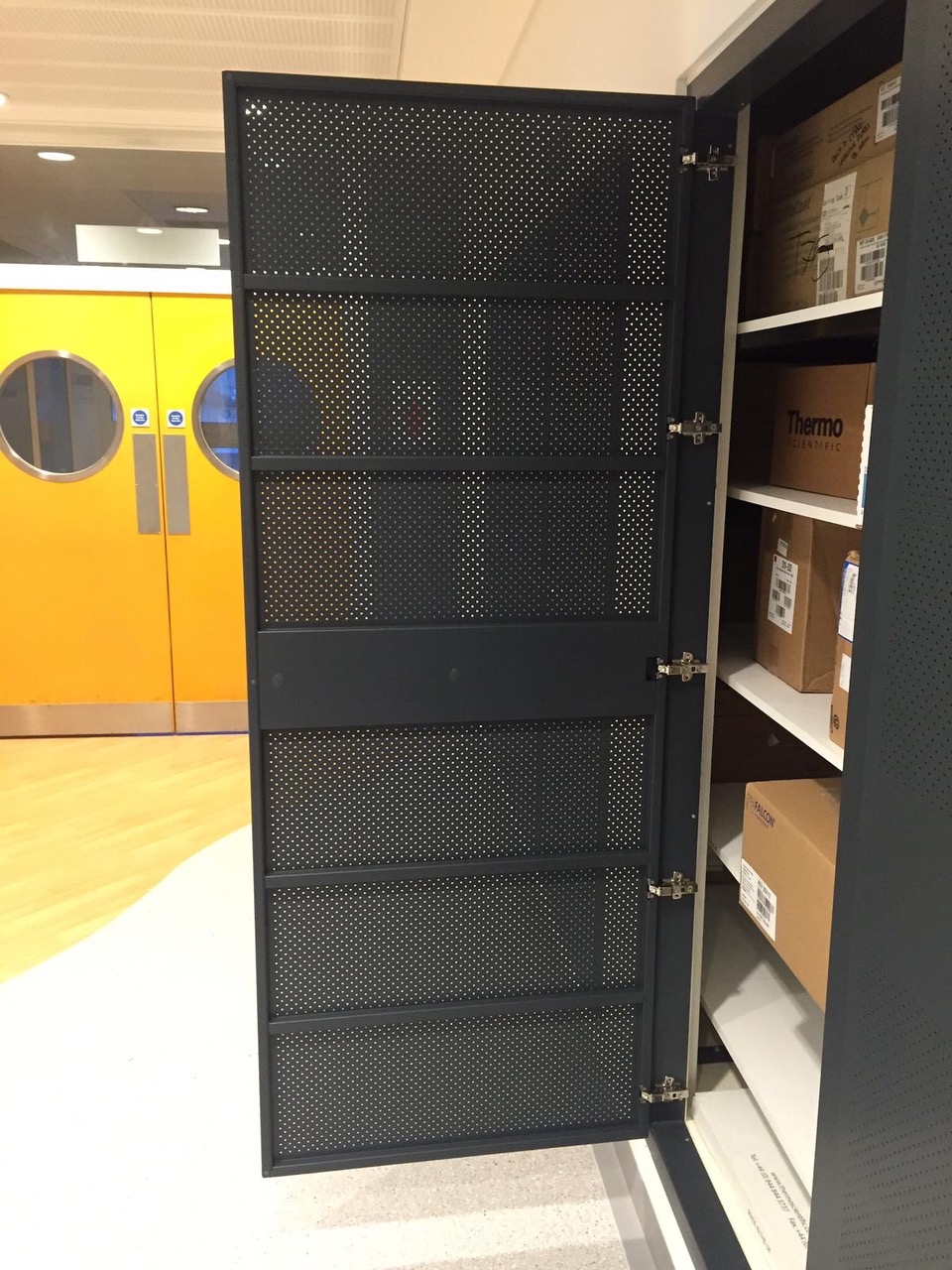
Things to remember when designing for CNC Punching
As we said earlier, your choice of punching machine must be led by the nature of your project, because:
- The list of materials that can be used on a CNC machine is pretty broad: from stainless steel and aluminium to brass and certain plastics. The ideal thickness ranges from 0.5mm to 6mm.
- The hole choice can be a simple rectangle or circle, or a bespoke cut-out pattern. Complex sheet metal component shapes can be created using single strikes as well as by overlapping geometric shapes.
Tips for CNC punching
Here are our top tips for getting the maximum out of your CNC punching:
- Ideally, hole diameters or rectangular slots should no smaller than the gauge of the material. It’s also best if the distance between holes / slots / edges is no less than the material thickness.
- Cluster tools can punch a number of holes in a grid at the same time, drastically reducing run times. This can be used very effectively for ventilation grilles or LED panels.
- Punch forming can produce some useful features very economically. Louvres for air vents, dimples for locating positions, bridges for slide rails or back stops can all be produced in a matter of seconds.
- As a CNC punch typically takes longer to set up compared to a laser cutter. Therefore, consider increasing your order volumes to reduce the unit price.
- If your part is two dimensional, ie flat and smaller than 90mm diameter (approx 3.5″), it’s possible to punch it in one stroke with custom tooling.
Is CNC punching right for my fabrication needs?
Only a punching machine can achieve geometrically-precise shapes to the highest levels of quality, without needle holes, spatter, waves or scratches. However, as we said at the beginning of this blog, deciding whether CNC punching is right for your needs rests with your design brief. What are your objectives? What are you wanting to achieve? What’s your budget and timescale? You need to consider if a simple alteration to your design brief will enable you to use this cost effective means of punching the desired shape(s) in your material? We regularly have these kinds of discussions with our customers. Therefore, please get in touch if you’d like some help working out your options.