Sheet metal welding – a major part of the fabrication process
We have 3 key welding considerations (see below) but first, let’s take a look at the issues:
Welding must feature at the design stage
To weld or not to weld – how do you decide?
If, for example, a design eliminates welding but makes the bending process incredibly complex, the design is flawed. However, adding unnecessary welding when a simpler option could be used, isn’t ideal either. Welding adds strength but it’s also another sequence in the process with all the implications of cost and labour. So, the implications and role of welding need to be considered right from the word go.
For example, one of our interior designer customers asked us to manufacture and install a large (3m sq) backlit metal sculpture (a logo as shown in the main image) in a reception area.
We worked with the designer to achieve their vision. Initial plans showed layers of tubing cut lengthways to create a channel within which the wiring for the LED lighting could be hidden. However, slicing tubing in half lengthways would be incredibly labour intensive. Another alternative, extrusion, would be expensive for a ‘one off’ structure because of the need for special dies.
Our solution was to replicate the tubing as a 3 ‘sided’ u-channel structure using a combination of CNC punching, CNC bending, rolling and welding. This enabled us to create the structure with the look and shape dictated by the design. Sprayed with black powder coating, assembled and installed with minimal fixings, the logo looked like it was floating on the wall which was exactly the effect the customer wanted.
What kind of stress is involved?
One of the key questions to ask is what kind of stress is involved, in either a structure or component, and where exactly is it located?
Take a simple L-shaped wall bracket for a shelf. A gusset, welded between the two faces would certainly add strength. However, if excessive weight is placed on the shelf, the force of the load is going to be directed toward the edge of the shelf which is weaker. The solution? Added support underneath.
The likelihood of welds cracking and failing is another stress-related issue, especially with aluminium.
Ideally, the material should be welded in a softer temper (e.g. T4), to avoid the metal becoming brittle and cracking under stress. Once the welding process is complete, the parts can then be age hardened (heat treated) to T6 condition. This ensures the parts are now at the right tensile strength but, more importantly, the welds will not crack and fail when under stress.
Managing distortion at the welding stages
Another consideration during the welding process is the possibility of warping and distortion. We made 3m long handrails for the first floor of a building to which the customer wanted a plate welded to the bottom to act as a ‘modesty panel’ to shield people from those looking up from the reception area.
The challenge was fully welding the plate to the handrails without the heat causing them to curve like a banana. Our solution was to clamp and pack the plate, temporarily bowing it in the opposite direction prior to welding. The heat from the welding would pull the plate back to square, nullifying distortion and maintaining the correct shape of the rails once the clamps and packers were released.
Alroys’ 3 key welding considerations
Whatever the size of your project, welding needs to be designed-in with these 3 key considerations in mind:
1. Find the purpose
‘Interrogate’ the brief – it’s a vital first step to understanding what the client has in mind so you can work out where and how welding is involved. It’s our starting point for creating structures and components that work efficiently, effectively and safely.
2. Put safety first
Safety is always top of our priority list so knowing the intended use of the component or structure is vital.
For example, is it structural? If so, it will have to be certified, which is why we are accredited to EN1090-2, a legal requirement when manufacturing anything structural.
This means all the materials we use are certified and traceable, and our welders are qualified. We also ensure that a qualified structural engineer determines the required thickness of the material, and the size and type of weld (‘butt’ or ‘fillet’) based on their stress calculations.
Take a set of railings in a public space, such as a football stand. They need to withstand the weight of a lot of people leaning on them. Welding and material strength are massive contributory factors to these railings being fit for purpose.
3. Don’t ignore the finishing treatment
Not all structures and components are hidden from view and even industrial environments need to look good. We create structures and components in offices and public space interiors so our workers are skilled at maintaining and replicating inherent textures such as brushed stainless steel.
Firstly, the welds need to be gently ground, usually with the aid of hand tools, to create the impression of radius corners. Next, burn marks are carefully brushed in the same direction as the grain in the material. Again, hand tools are used (such as a straight grainer) or elbow grease and a light grit Scotch Brite.
These processes may seem straightforward but it’s real skill and care that removes all signs of welding and the polished area matching exactly the original grain of the material.
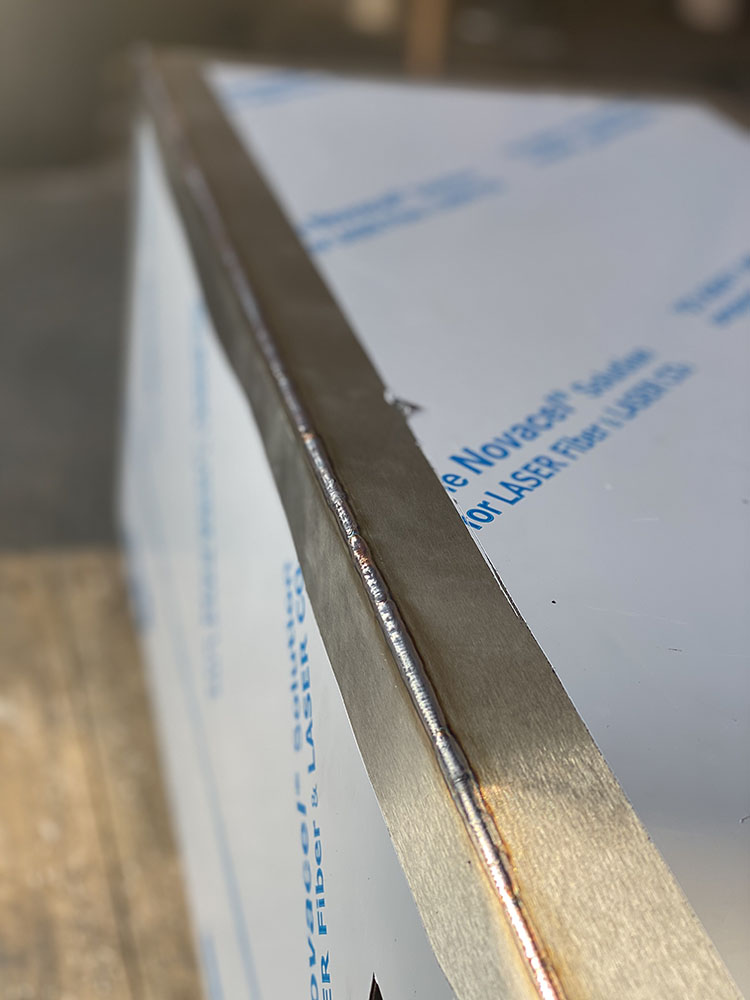
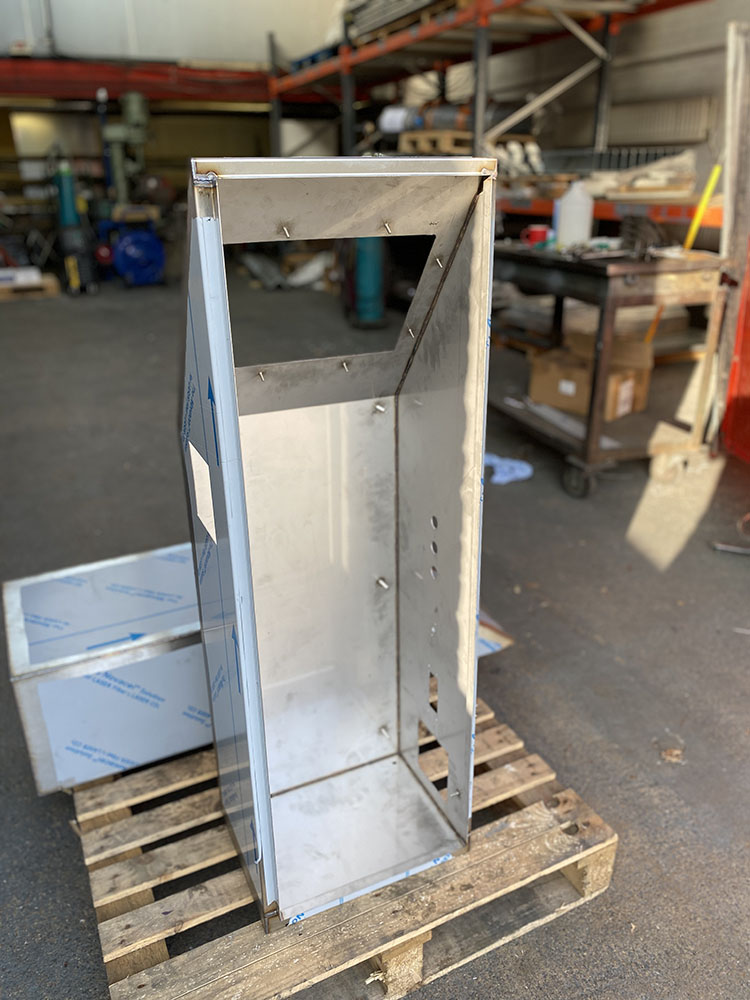
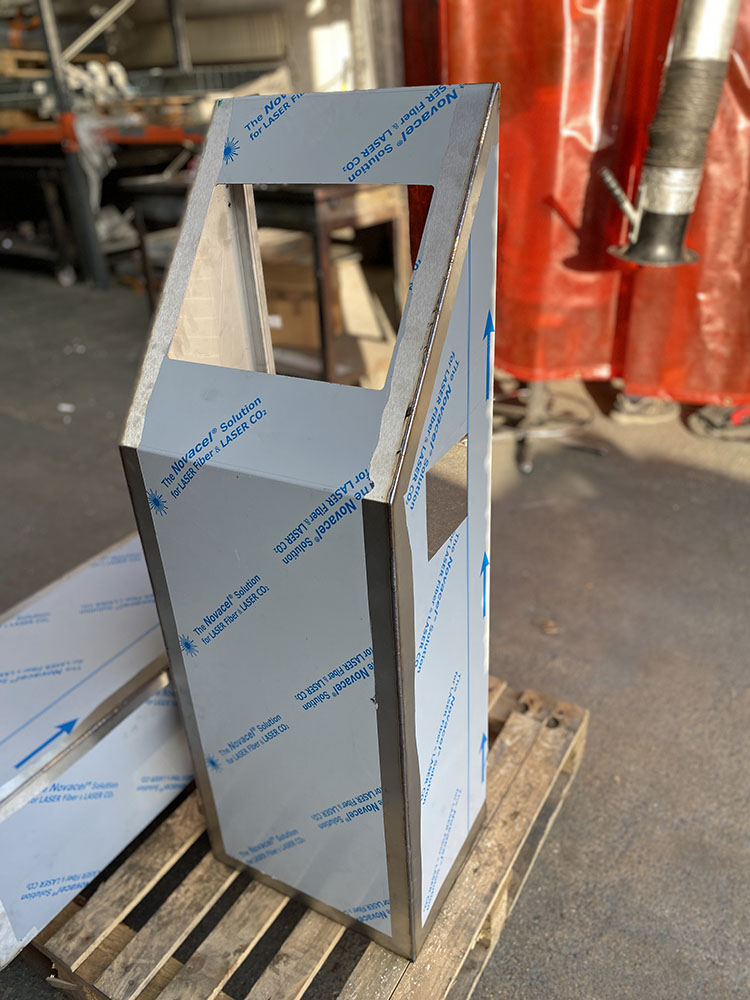
Burn marks from welding spoil the look of the cabinet.
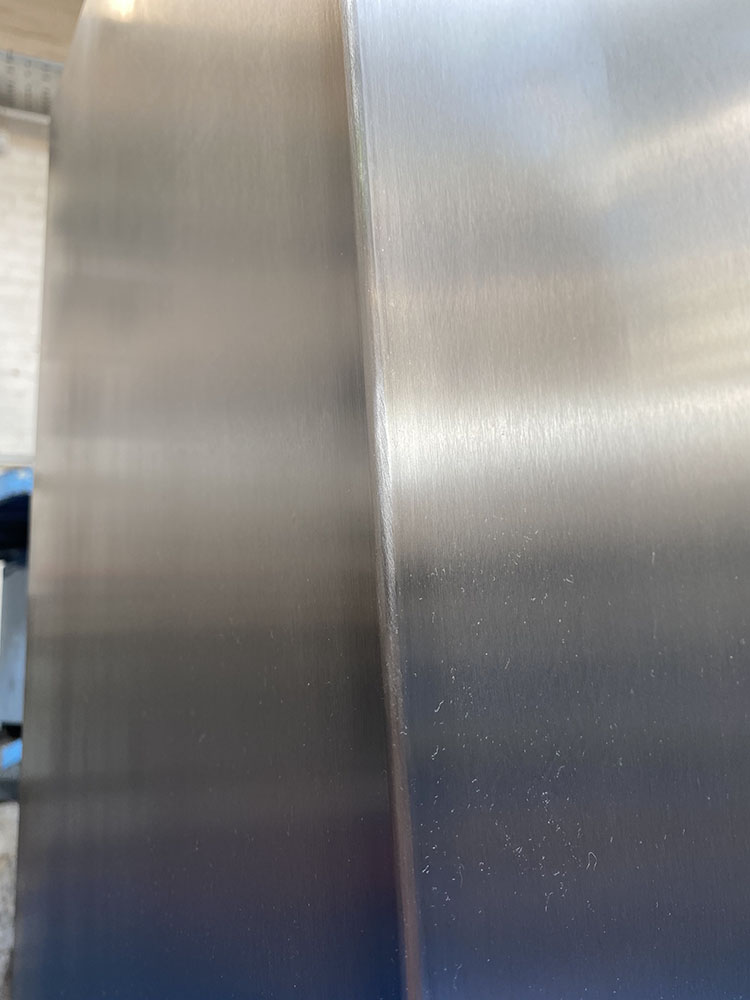
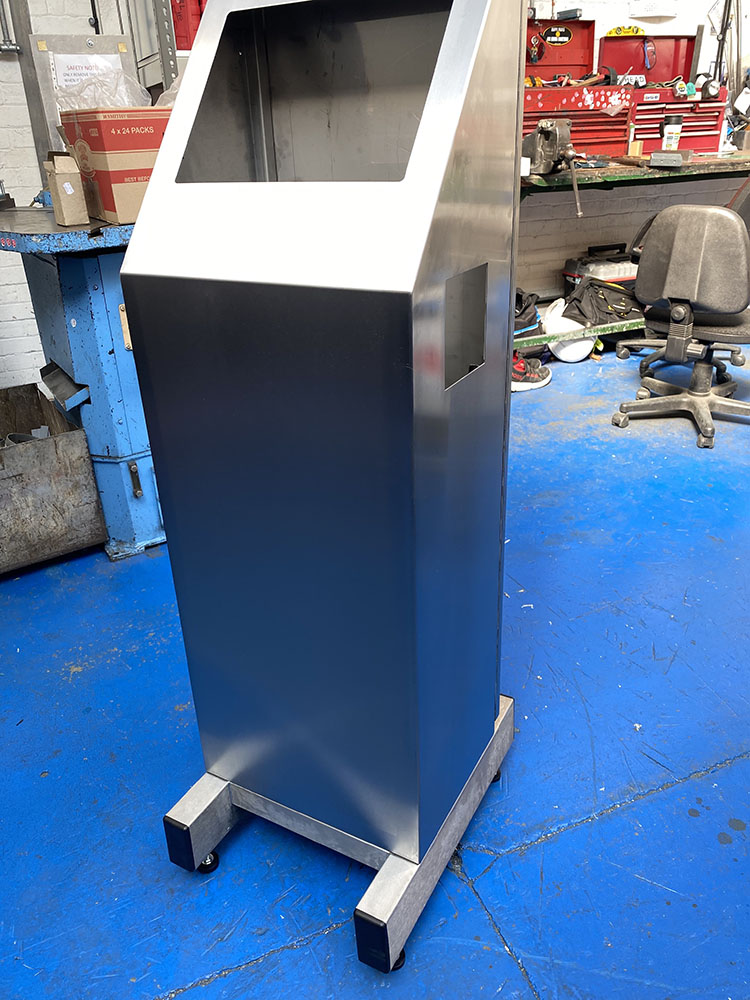
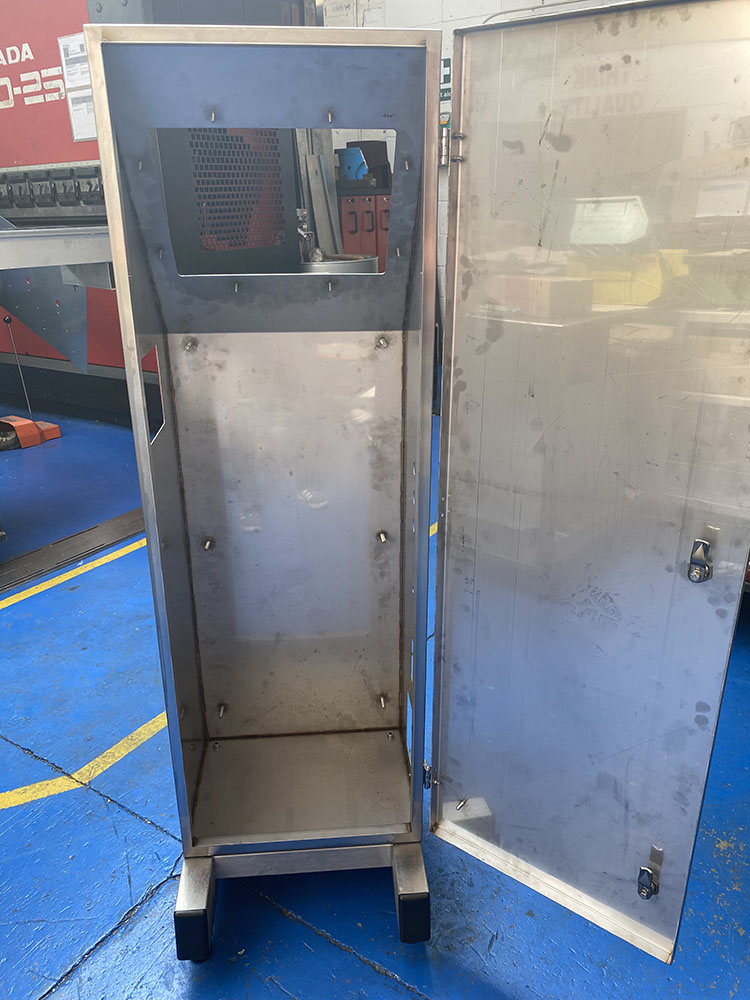
All signs of welding polished out to match exactly the original grain of the material.
Design-in welding
Fatigue in welded structures and components is the most common cause of failure and it’s usually attributed to poor design. Such failures can prove to be expensive, in terms of lost production, repair cost and even danger to life.
We always look behind the brief and question assumptions because the design of a part or structure should exploit the advantages of welding and minimise its disadvantages.
Further reading: EN1090-2 Steel fabrication.