What is customised metal fabrication?
Custom Metal Fabrication for Bespoke Solutions
Alroys is a customised metal fabrication company. We specialise in one-off bespoke pieces and relatively small production runs. Our projects range from large structures such as railings, canopies and walkways, to smaller, interior design pieces where metalwork is a key feature. Typically, our customers work in a variety of industries, especially aerospace, construction, architecture and interior design.
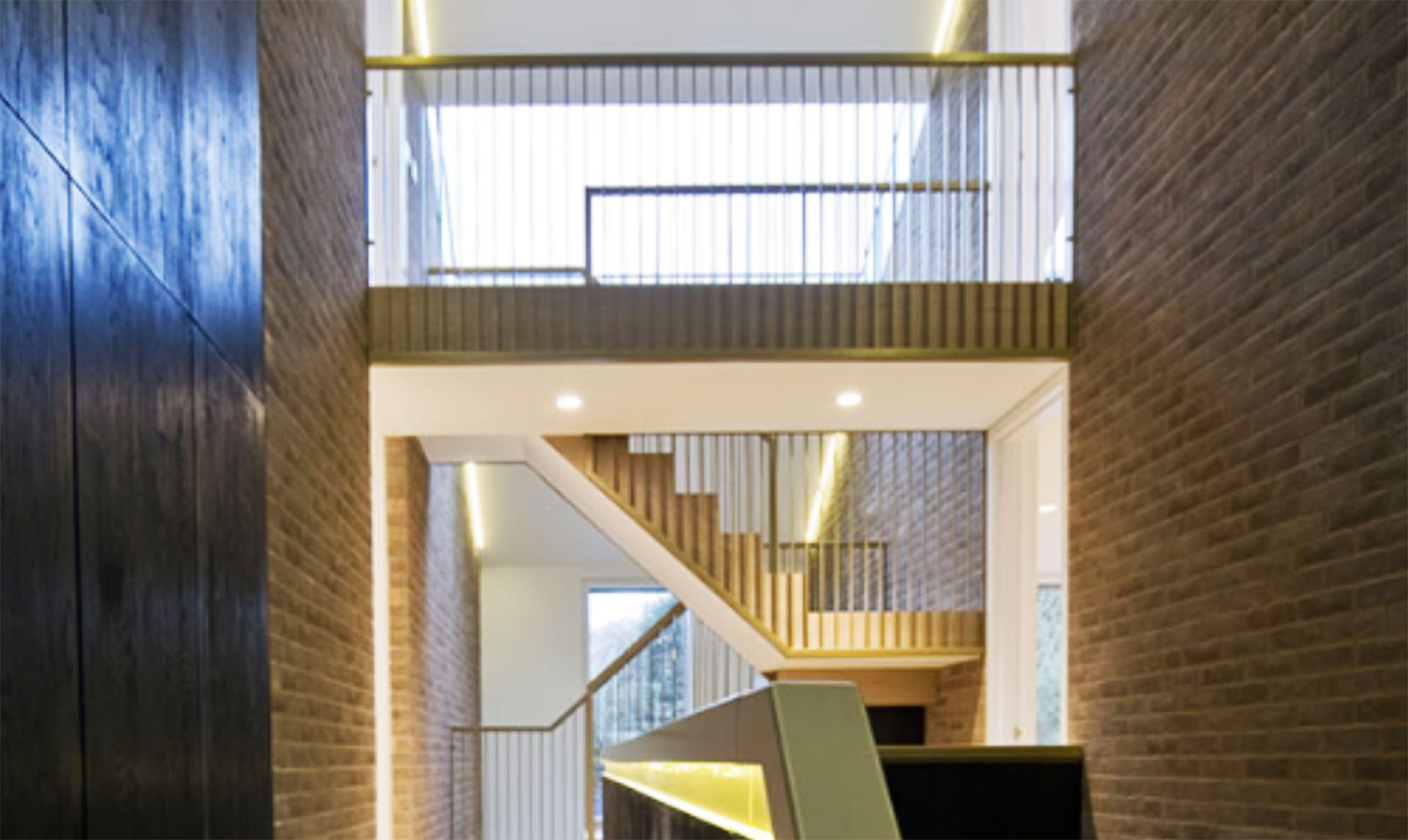
What is customised metal fabrication?
Customised metal fabrication is where we work to a precise design, as opposed to a ‘off the shelf’ solution. With bespoke metal fabrication projects, our customers often need our help to ensure they achieve their very precise objectives. Sometimes their plans and visions present unique challenges. Solutions emerge through our knowledge, experience and critical eye for detail.
Our team of skillful and experienced technicians is the key to our success. It’s a collaborative process with the client, covering these 6 stages:
1. Design
2. Prototyping
3. Programming
4. Fabrication
5. Metal finishing
6. Assembly and installation
Let’s take a brief look at each stage, and the kind of personalised service our customers can expect:
Design
Whatever the scale of any project, a fit-for-purpose design will lead to a successful outcome. Our customers’ objectives range from performance and functionality through to cost savings and environmental needs. We focus a lot of time and energy at the design stage in order to anticipate and eliminate problems later in the manufacturing process.
For example, an architect might need some ‘wow’ factor added to a high-end residential property – a stunning, bespoke staircase, for example. The metal fabricator has to interpret the architectural vision. He then converts it into a manufacturing process that will produce something structurally sound as well as stylish and on brief.
Precise measurements and evaluation of the installation site – prior to design and manufacture – is vital. This will eliminate many problems which, when encountered later on, could cause costly delays. The installation stage (see below) often throws up its own challenges so it’s important to design-out any major alterations or need for re-positioning as early on as possible.
Prototyping
Producing a prototype is another way of ensuring the best possible outcome for a project. It tests the feasibility of a custom design so you can see how it works, how easy (or difficult) it is to manufacture, and how long it takes. Prototyping allows you to test how the chosen material will behave, and whether a cheaper version might be up to the task. Prototyping isn’t necessary for every custom project. If your production run is as many as 1,000, producing 1 or 2 for final testing is the logical thing to do.
Programming
Once the design and prototyping stages have been completed to our satisfaction, programming ensures the optimum process is undertaken, from reducing waste to improving delivery times. Laser cutting, for example, is a flexible and cost effective process. A variety of materials – steel, aluminium, brass and copper – can be cut into very complex shapes and apertures with tolerances accurate to +/- 0.1mm.
Fabrication
Most fabrication projects involve pre-formed materials, such as angle, bar and box section. Bespoke parts are then fabricated using various methods, including cutting, drilling, grinding and welding. Ongoing advances in technology means the speed and quality of workmanship is forever advancing. For example, programming a CNC machine to cut, drill and punch sheet metal.
Metal Finishing
Selecting the right finishing process, such as powder coating, depends upon the need for environmental protection, aesthetic finish, and the type of metal involved. Cost effectiveness is another consideration. Some processes may be expensive but enable greater speed of final delivery.
In some cases finishing might be a process of trial and error. We created an ornate table for an interior designer that involved tortoiseshell panelling and a black painted table top with pheasant feather inlay. It wasn’t until we presented the designer with the finished product that they knew it worked and was exactly what they wanted.
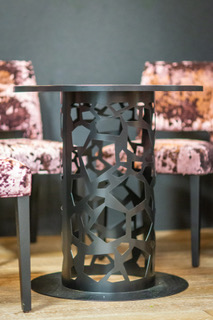