What is
galvanised
steel?
What is galvanised steel?
Galvanised steel is where the metal is coated in zinc to give it a significant amount of protection and, therefore, durability. Bare metal surfaces are prone to corrosion because they contain iron that oxidizes when exposed to oxygen. The zinc protects by acting as a ‘sacrificial’ coating that steers corrosion, such as rust, away from the metal. There are several galvanising processes available, the most popular being hot-dip. The result is a long-lasting and high-quality formable metal – steel, iron or sheet aluminium – for application across a wide range of industries.
In this blog, we give a comprehensive answer to the question ‘What is galvanised steel’, detailing the types of galvanisation, pros and cons, and typical applications.
Types of galvanisation
There are two main galvanisation processes: hot dip and electro galvanising:
1. Hot dip galvanisation
Simple and economical, hot-dip is the most widely used method of galvanisation. As the name suggests, it involves dipping the steel into molten zinc at a temperature of about 860°F (460 °C). The zinc and metal are bonded once zinc mixes with oxygen from the atmosphere turning it into zinc oxide. This then reacts with carbon dioxide to form zinc carbonate which creates the final coating on the base metal in the form of a crystalline-like pattern on the surface.
2. Electro galvanisation
Electro galvanising is an electroplating technique whereby the metal is immersed in a solution containing zinc salts. This is followed by the application of electricity to induce an electrochemical reaction. Compared to hot dip galvanisation, electro galvanising creates a thinner coating, ideal where profile or aesthetics are important. Steel sheets and wires are often electro galvanised and commonly used in the automotive and domestic appliance industries.
The pros and cons of galvanised steel
There are three significant advantages:
- Long term durability: galvanisation affords up to 35 years’ protection from corrosion before maintenance (or at least inspection), is required. Then, galvanised coatings can be examined by eye, and their thickness tested using simple, non-destructive methods.
- Environmental qualities: zinc, being a natural material, does not emit harmful toxins. Furthermore, if properly salvaged to retain its durability, galvanised steel can be reused time and time again.
- Affordability: galvanisation is a cost-effective means of applying protection in itself. Combined with its durability and sustainability credentials, it’s an extremely economical material for a variety of industries and applications.
Disadvantages can be summed up as follows:
- The protective layer of zinc also rejects paint so cleaning the surface with something acidic, like vinegar, is necessary. Then paint, specially designed for galvanised steel, can be applied.
- Despite its longevity and corrosion resistance, galvanised coatings are still susceptible to chips and scratches which is more of an aesthetic rather than performance problem.
- Care needs to be taken when mixing galvanised steel with other metals to avoid ‘galvanic corrosion’. For example, when combined with brass, ‘dezincification’ can be triggered. This is a form of corrosion and weakening whereby zinc is dissolved out of the brass alloy
- Oxygen, moisture, and dissolved salts present in soil means corrosion can be accelerated. Consequently, galvanised steel is preferred for structures that are partially exposed to the atmosphere and partially buried.
- Galvanised steel and copper cannot be connected to each other as the two can produce a chemical reaction that weakens the joint.
- In older homes, galvanised steel also poses a risk due to its lead content (eg in pipework), which has been proven to be unsafe for both children and adults.
Galvanising process
The steps in the hot-dip galvanising process are as follows:
1. The steel is cleaned in a degreasing solution.
2. After being cleaned, the steel is ‘pickled’ in a vat of diluted hot sulfuric acid.
3. The steel is then fluxed in an aqueous solution (typically zinc-ammonium chloride).
4. After the flux, the steel is galvanised through immersion in a vat of molten zinc.
5. Post galvanising treatment is the final process, which can include quenching into water or air cooling.
For electro galvanising, the process involves a layer of zinc being bonded to steel (electroplating) by running a current of electricity through a saline / zinc solution with a zinc anode and steel conductor.
With both processes, the steel must be inspected carefully to ensure a complete coating, thereby ensuring durability for the maximum length of time before inspection is necessary.
Typical applications
Due to its strength, durability and resistance to corrosion and aggressive environments, use of galvanised steel has become widespread in many industries and manufacturing sectors. Galvanised steel is used for structural elements and parts in almost all areas of industrial and civil engineering construction. It’s present in many everyday structures from buildings, cars and bicycles to roofing, facades and ventilation systems.
Some specific uses of galvanised steel are as follows:
Wind and solar industries
Solar projects need uninterrupted performance once installed because any repairs / maintenance result in serious disruption to service (aka revenue loss). So corrosion-resistant galvanised steel with its environmental credentials, is ideal for wind and solar industries.
Harsh environments
The agriculture industry demands tough, resilient equipment that lasts for decades, even when exposed to harsh environments. Galvanised steel is used in urban and rural areas, especially in severely exposed and coastal environments.
Automotive industry
Galvanised steel makes up about 80% of the body of a car allowing the car industry to provide ‘anti-rust warranties’ to customers.
Construction Industry
The durability of galvanised steel has made it a popular choice in the construction industry for over a century. It’s used in both commercial and residential properties, on a large and small scale. Apart from providing the structure and framework, galvanised steel is often the sole material used such as for agricultural and commercial storage. On a smaller scale, the combination of durability and contemporary ‘feel’, makes it popular with architects for balconies, verandas, staircases, walkways, etc.
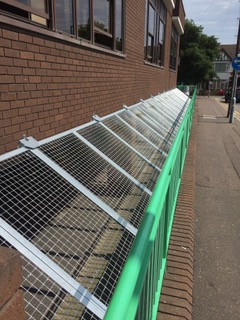
Telecommunication industry
In the telecoms industry, galvanised steel is highly valued for wiring and equipment boxes and casings, thereby reducing the risk of damage to property and the need for constant maintenance.
Galvanised steel: the durable, sustainable and economic choice
Galvanised steel is a firm favourite across industry sectors – for good reason. Durable and sustainable, it represents a very cost-effective and versatile material. As you would expect in our industry, guidance from a fabrication specialist is vital to ensure the right material and process is selected for your project. That’s a role we fulfil for all our customers as part of our sheet metal services.
Get in touch to discuss your project especially if you need a clear, concise answer to ‘What is galvanised steel’ and how you can make good use of it.