What is a sheet metal gauge?
How does it ensure fabrication and components are cost effective?
How do you ensure you’ve chosen the correct thickness of material for your component and fabrication projects? You use a sheet metal gauge which, depending on the nature of your project, will guide you in your selection so that fit-for-purpose is met. We create metal parts and structures for clients across very different industries. These include, medical, telecoms, aerospace and construction. Being certain that every aspect of our work will withstand the rigours of usage in various environments is why our clients rely on us to meet their sheet metal and fabrication needs. One of our tools, in this respect, is the sheet metal gauge.
Brief history of the gauge system
The gauge is a traditional means of measuring material thickness. It originated in the British iron wire industry to measure diameter. These days, electrical cables are generally measured in square millimetres of cross-sectional area. However, standard wire gauge (SWG) is still used for measuring the thickness of sheet metal.
Your choice of gauge for sheet metal is either a caliper or ultrasonic, together with the charts according to the material (eg metals) you are using.
Types of caliper gauge
Calipers are mainly used to measure the internal diameter of tube or cylinder as well as the length of an object. There are three types for measuring the gauge size of sheet metal:
- Vernier
- Dial
- Digital
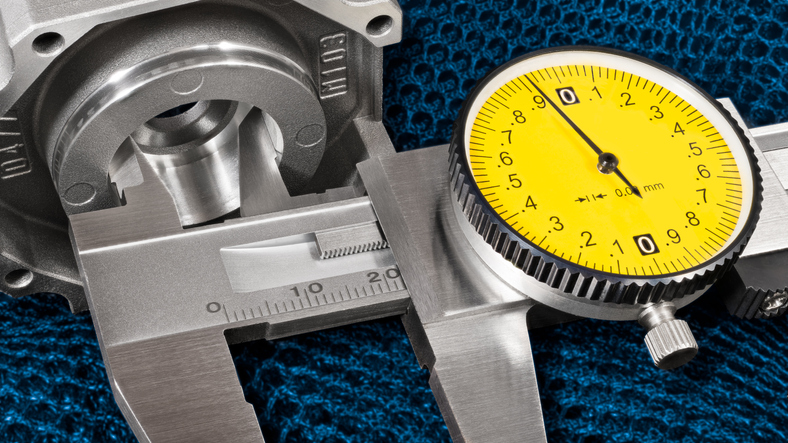
Vernier Caliper
This particularly useful when you need to measure something round (eg tubing) to the nearest 0.02 millimetre or 0.001 inch.
Dial Caliper
The dial caliper measures to the same level of accuracy as the Vernier, using a dial to show the final fraction of an inch or a millimetre.
Digital Caliper
Digital calipers use linear encoders to measure internal and external distances in both metric and imperial conversions.
Ultrasonic Gauges
Ultrasonic thickness gauges work by measuring how long it takes for a sound pulse that has been generated by a small probe (ultrasonic transducer) to travel through an object and back to the meter. The velocity of sound in the particular object is an essential part of this calculation. Different materials transmit sound waves at different velocities. This is generally faster in hard materials and slower in soft materials. Sound velocity can also change significantly with temperature. For this reason, it’s always necessary to calibrate an ultrasonic thickness gage to the speed of sound in the material being measured.
Measuring sheet metal thickness using a gauge
The gauge number is the independent value that determines the thickness of sheet metal in terms of inches or millimetres. The higher the number, the thinner the sheet metal. Ferrous metal has a different gauge from nonferrous (such as copper) for which the unit of measurement is ounces per square foot.
Standard sheet metal gauge chart
To ensure you have the right gauge for your projects, compare the thickness of your metal sheet to a conversion chart, such as the one below. For example, if you need to gauge steel, there are a number of options open to you.
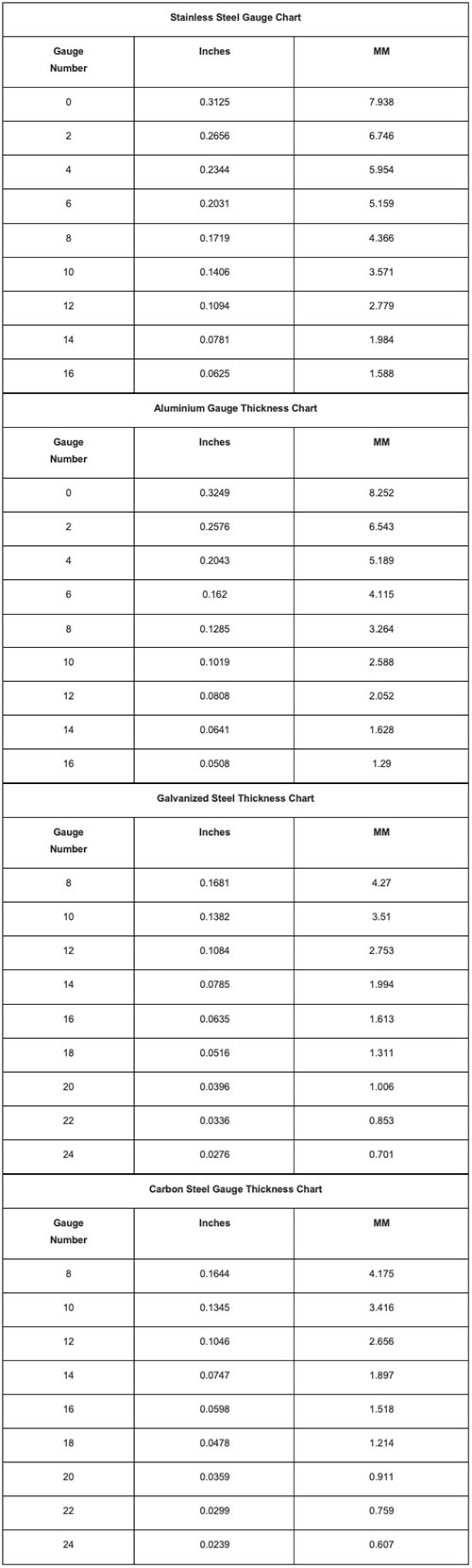
Importance of choosing the correct gauge in sheet metal fabrication
We summarise the importance of choosing the correct gauge in sheet metal as follows:
Durability: gauging the right thickness of your material has the single most impact on the durability of your part of structure. A construction project involving high rigidity and strength, requires a lower (thicker) gauge sheet material. The same applies if your structure, or part, is to be subjected to harsh environments. If, however, different curves and high flexibility are involved, a higher gauge material (thinner) material will be important.
Economy: the thicker the metal the higher your production and shipping costs so specify thinner material if at all possible – eg, if a part isn’t under pressure in any way, including from the weather.
Efficiency: fit-for-purpose is a key consideration for Alroys, and specifying the right material thickness is integral to the success of both fabrication and component design.
How to decide the right gauge for sheet metal fabrication
As we detailed above, the right thickness of material depends upon the nature of your project and exactly what you want your fabrication structure (or part) to achieve. Whichever type of gauge you use (caliper or ultrasonic) you’ll also need to refer to a conversion chart for ferrous or non-ferrous metal. Very briefly, the difference between ferrous and non-ferrous metals:
Ferrous metals
Common ferrous metals include engineering steel, carbon steel, cast iron and wrought iron. These metals are renowned for their tensile strength and durability. Carbon Steel (aka structural steel) is a staple in the construction industry. This is for skyscrapers and bridges etc. Ferrous metal is also used in shipping containers, industrial piping, automobiles, and many commercial and domestic tools.
Non ferrous metals
Non-ferrous metals include aluminium, copper, lead, zinc and tin, as well as precious metals like gold and silver. Their main advantage over ferrous materials is their malleability. They also have no iron content, giving them a higher resistance to rust and corrosion, so they’re ideal for external fabrication projects. Non-magnetic, nonferrous metals are also important for many electronic and wiring applications.
How Alroys can help
The way we work with many of our clients is the most advantageous because we discuss their project with them at the design stage. This means we can advise on the best way of achieving their aims. The type and thickness of the metal used in a project is a vital part of this success. You can read more about accurate fabrication specifications or get in touch with us direct to discuss selecting the right sheet metal for your project.
Want to discuss your next project?
Contact us today and get started.